For Problem 4, me and Nesreen had to come up with a solution to construct and plan the scenery for “Mary Martin”. Most of the scenery is being constructed by John Creech Design and Production Incorporate. Compared to the previous two projects, this definitely gives us less stress for the drafting phase. For the problems itself;
1. We had to figure out how the suitcase is going to be carried on stage.
2. How one of the picture frames are going to be projected on stage.
For the suitcase, my idea was to create a prototype test to figure out the proper fold.
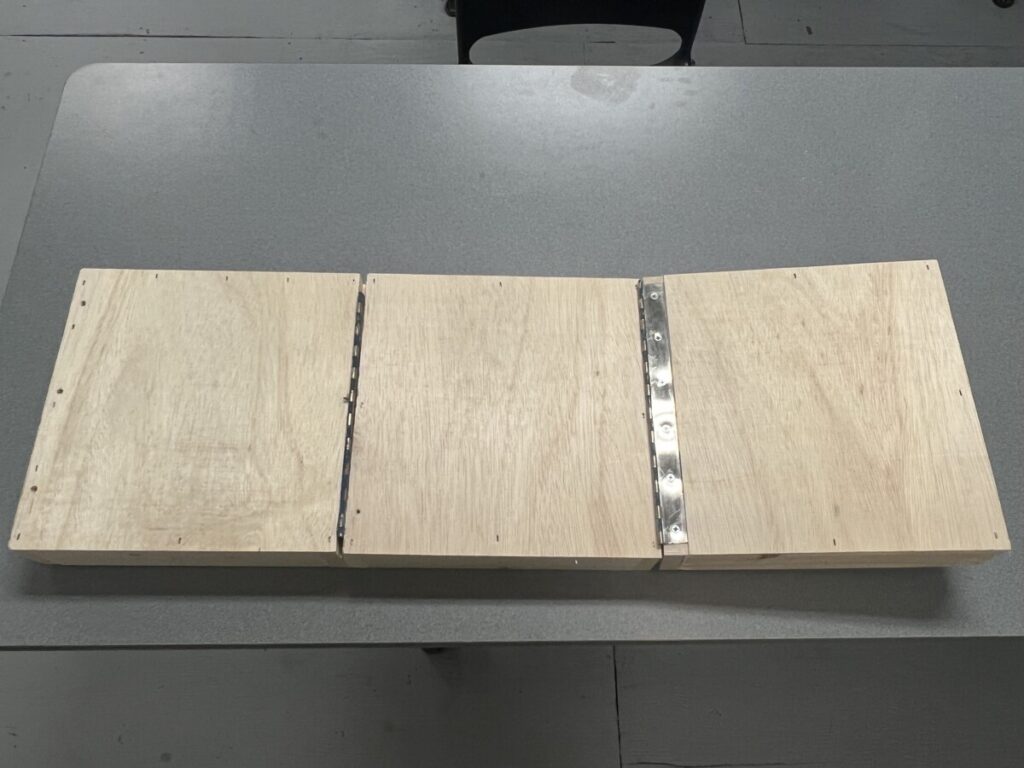
What I decided to do in this test piece was to utilize piano hinges for the flats to fold into itself. For the flats itself, I took some scrap lumber from the scene shop (1×3 Ply) and created small squared flats. Once I stapled in all the framing members, I also applied lauan face cover to represent the suitcase’s exterior. In this test piece, I decided to do two different placements for the installing of the piano hinges. One flat would have the hinge on top and the other to the side. The flat to the left would have the piano hinge connected to the side to the one in the middle. The process of installing the piano hinges involves in scraping off material with a router. To take some of the material off from the flats, I used a 3/16″ drillbit and applied a fence with a stopper for the flats to be run on. After scraping the flats, I took the piano hinges, measured the holes onto the flat and drilled some holes for mechanical flat head screws to be placed. The reason why you want flathead screws to be placed on the piano hinge is for maximum rotation. The flat itself would also be blocked from the other to prevent the proper close. Turns out, the first example of the left of the picture is the most effective way to properly fold a flat inwards. The other example on the right isn’t the most proper because it doesn’t close all the way. For that reason, keeping the hinges inwards helps seal the flats to fold in itself.
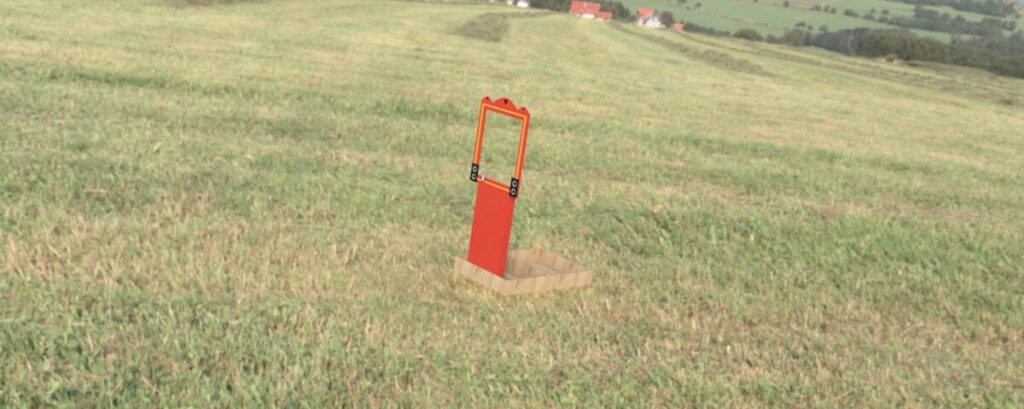
On the construction drawing for the suitcase, one of the most difficult problems was finding out how to keep the kissing booth standstill after transforming. Despite not showing this on the ePortfolio, one way to allow this to work is to use footers to keep the kissing booth in tact. For the detail itself, you really want the suitcase to be light as possible. I tried to make the suitcase as realistic as possible by drafting it in Fusion 360. The baseboard for the suitcase is made up of 1×3 ply with lauan facecover. The stand itself is also made out of the same material as the baseboard. The difference is that the stand will be painted with Regal Select Interior Paint mixed with flameproof adhesive. For the top part aka the Kissing Booth, there’s a whole lot of detail to be defined. For the speakers itself, the material would be made out of baseboard. With the diaphragms, the material would be also the same. But to get the circular shape, using a jigsaw with a circular jig would help recreate it. Once the shape is created, using narrow crown staples and glue would help reinforce it. In the center of the framing, it mimics as an LED strobe light. For the material, I would use PVC foam to put in the center. The suitcase would also have locking hinges to lock it in place. After listing all the materials, the suitcase should be light enough to carry.
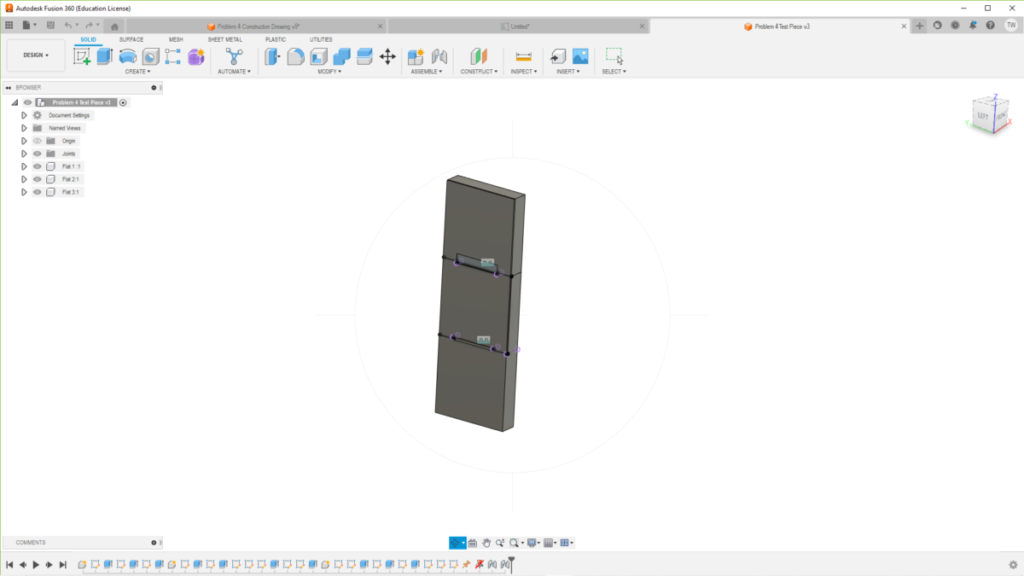
For the second part of the problem is dealing with the projector being rolled on stage. For this to happen especially if handling a load-in/load-out, using cart smart casters with core wheels and a locking mechanism is ideal for this job. One important tip is to make sure there’s enough room for the casters to sit on when attaching it to the framing of the projector. Materials included should be 1″ Philips Steel Flat Head Screws, 3/16 hex bolts and 1/2″ fasteners. Another thing is to make sure the casters are swivel to prevent constrained movement in a linear direction. You want as much free movement as possible when pushing the platforms onto the stage. To keep the platform in place is using a stop block. The material of the casters is depended on the material of the stage floor. If the stage floor is made out of concrete, a good recommendation is steel wheels because of less abrasion and pressure. In this case, were using core wheels because the stage floor is not made out of concrete and instead made out of a softer material like black sprung wood covered layered with marley.