- 1. PROJECT PLANNING
- General Coordination
- Site Logistics
- Q1: What reasons might you have to select equipment that was NOT the most efficient for the work at hand?
- Labor
- Materials
- Regulation / Authorities
- Staffing
- Scheduling
- Q2: What problems come up on construction teams that fail to honestly assess the requirements and constraints of a project Q3: What is a long lead item and how may it affect project planning? Give two examples of long lead items commonly found in construction projects. Q4: What is the purpose of a site logistics plan?
- 2. SCHEDULING
- Reading a Schedule
- Q5: In a typical Gantt Chart schedule, where do you look to find a list of activities and their sequence?
- Q6: In a typical Gantt Chart schedule, where do you look to find the durations of activities?
- Schedule Organization
- The Critical Path Method
- Look Ahead Schedules & Jobsite Coordination
- Schedule Disputes
- 3. REVIEW
1. PROJECT PLANNING
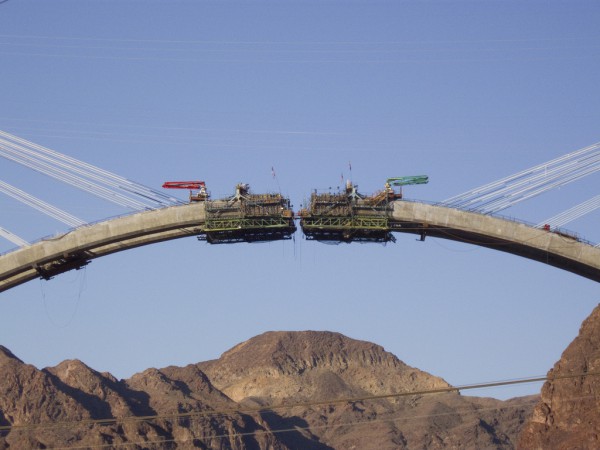
Hoover Dam Bypass Bridge Construction 3
Construction of the Mike O’Callaghan-Pat Tillman Memorial Bridge at the Hoover Dam. Taken July 5, 2009.
Via Alan Stark
Planning for a project involves using past experience to develop a strategy for a new project based on its requirements. Successful project planing results in a more efficient, less confused building process. To be successful, a project planner must honestly address the requirements (necessary features) and constraints (limiting elements) of a project and its participants. Failure to do so may lead to schedule overruns, cost overruns, and project performance failures.
Use your project plan and schedule to communicate the reality of the project to the other participants. Communicate what will happen, when, and who will be responsible for it. Communicate completely and transparently. Do not make assumptions about what other team members should know, understand, or be responsible for.
Once a project has been initiated, operational planning and scheduling are usually the responsibility of the construction team. The organization and control of project work is operational planning, while scheduling is the process of breaking a project into tasks and determining the duration and relationship of those tasks.
Operational planning covers topics such as:
General Coordination
- Contract language
- Coordination among contractors
- Interdependency of tasks
- Document control, management, and distribution
- Special equipment requirements
- Time allowed for construction
- Work times
- Utility interruptions
- Temporary utilities and its construction
- MBE WBE, VBE, or LBE requirements
Site Logistics
- Site security
- Work, equipment, & storage areas
- Impacts on traffic and transit
- Pedestrian routes
- Temporary access for obstructed surroundings
- Deliveries to jobsite
- Refer to sample: Site Logistics Plan_Foundation
From the American Institute of Steel Construction, Crane Selection and Application (2006),
Principles that govern crane selection (a Powerpoint presentation. Scroll through the slides):
Notice the following statement:
As with most types of construction equipment, the theoretically optimal crane for the job based on capability may not be readily available, or a more capable crane that is owned by the steel erector may be more economical
Availability will always be an important factor in crane selection
Q1: What reasons might you have to select equipment that was NOT the most efficient for the work at hand?
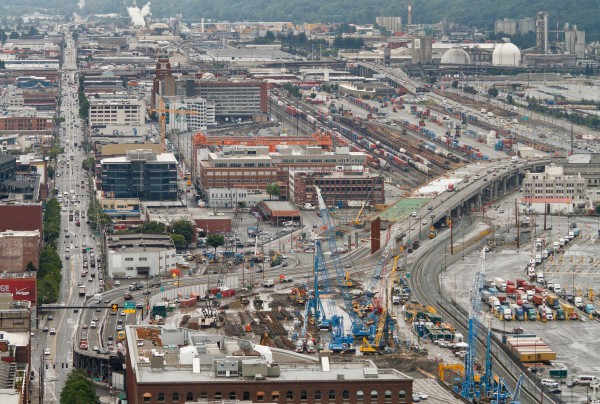
Viaduct replacement construction snapshot – July 20, 2012
Looking down at the heart of the construction zone for the replacement of the Alaskan Way Viaduct. In the foreground is construction on the SR 99 tunnel boring machine launch pit. Just to the south you can see future northbound lanes of Highway 99 taking shape next to the southbound roadway. The southbound roadway will carry both directions of traffic until the northbound lanes open this fall. See the same location a year earlier.
Via Washington State DOT
Labor
- Labor availability
- Labor skill and training requirements
- Labor jurisdictions
- Payroll management / oversight requirements
- Site management of labor
- Union requirements
Materials
- Long-lead purchases
- Submittal tracking
- Material compatibility
- On site quality control
Regulation / Authorities
- Building Department requirements
- Environmental controls
- Safety controls
- Inspection requirements
- Special regulations / authorities
Staffing
- Site office
- Field office
- Provisions for all staff
- Organizational chart
Scheduling
Scheduling is covered in the next section.
Q2: What problems come up on construction teams that fail to honestly assess the requirements and constraints of a project
Q3: What is a long lead item and how may it affect project planning? Give two examples of long lead items commonly found in construction projects.
Q4: What is the purpose of a site logistics plan?
2. SCHEDULING
On scheduling, one industry veteran says:
Please don’t ask me to tell you what I will be doing next week. I am not quite sure what I am doing right now. However, I can tell you, to the day and hour when our three year, $100-million project will be complete.
Fredric L. Plotnick
(Read more from Plotnick: September 17, 2009 – ENR – Scheduling on Time.)
The schedule document is a tool – a visual representation of the project’s sequence. Scheduling is the process that results in that document. Scheduling can help you determine which activities are critical, which can be delayed, and the project’s duration. The schedule can be used in many different ways, including (via David Pierce, Southern Polytechnic University and a consultant to R.S. Means):
- Owner program planning
- “What if” Analysis
- Project Coordination
- Analyze and document project changes
- Resource Management
- Project Reporting and Monitoring
Reading a Schedule
The following slides give an overview of the information contained in a schedule and several typical schedule formats.
Q5: In a typical Gantt Chart schedule, where do you look to find a list of activities and their sequence?
Q6: In a typical Gantt Chart schedule, where do you look to find the durations of activities?
Schedule Organization
A schedule can also be represented in many different ways but its basic form should represent a list of activities, their durations, and the relationships between them. The schedule should be organized and logical.
The relationships between tasks are referred to as dependencies, and their are four task dependencies commonly included in project schedules:
Each task dependency is named and described by the relationship between the predecessor and its successor. For more information on these task dependencies, refer to Understanding Task Dependencies in Project Management (2016).
Finish to Start relationships are most commonly used in scheduling and are easiest for project participants to understand when reading your schedule.
The Critical Path Method
Critical Path Method (CPM) scheduling was developed in the 1950s. It creates a model of the project based on:
- A list of activities, usually organized by Work Breakdown Structure (WBS).
- The duration of each activity.
- The dependencies between the activities.
- End points, milestones, deliverables.
CPM calculates:
- The longest path of planned activities to the end of the project.
- The earliest and latest that each activity can start and finish without making the project longer.
Look Ahead Schedules & Jobsite Coordination
Look ahead schedules bridge the gap between overall project scheduling (showing the planned durations of all tasks through project completion) and the daily task management of your workforce. A look ahead schedule, usually created in increments of one, two, four, or six weeks, is a short document describing detailed tasks meant to be completed in the short term future.
A sample Two Week Look Ahead Schedule from Walsh Brothers, Inc. (2011):
A sample Two Week Look Ahead Schedule from Trinidad Construction (2013):
Schedule Disputes
An unreasonable schedule is a schedule with an unrealistic completion date. Unreasonable schedule requests increase cost of construction because of the following types of added costs:
- Premium costs and overtime labor to complete on schedule
- May pay more for RT labor in order to attract enough skilled workers to the job
- Bids will include extra money to cover possible damages
- Bids may be difficult to evaluate based on varying interpretations of the risks involved
- Poor guesses on availability of materials and equipment
- Disputes and paperwork.
To avoid unreasonable schedule requests, incorporate as much contractor input as possible in the early stages of project planning. Reach out to vendors and manufacturers whose products are specified and discuss product lead times. Discuss labor availability and subcontractor workload during the bid leveling and award phase to ensure that required companies and personnel are available during the project’s schedule.
3. REVIEW
Time for some review material. Listen to the follow podcast on creating a great schedule: 009 Creating a Great Construction Project Schedule – Cesar Abeid
AND
review scheduling concepts here: Planning and Scheduling Review – Gould.