- 1. THE SPECS
- The Project Manual
- Q1: What documents are part of the Construction Documents in addition to the specifications?
- Q2: Who compiles the specifications?
- Need for Specifications
- Q3: Why is it suggested that a specification be written to the level of a brighter than average seventh grader?
- 2. FORMAT
- Part I – General
- Part II – Products
- Part III – Execution
- Samples
- Spec Selection & Writing Tools
- Performance vs. Prescriptive Specifications
- Q4: Define performance specification and explain why one might be preferred.
- Q5: Define performance specification and explain why one might be preferred.
- 3. AVOIDING CONFLICTS
- 4. SUBMITTALS
- Q6: How do submittals differ from contract documents even though they require approval by the Architect on behalf of the Project Owner?
- 5. SPECS AND ENFORCEMENT
- 6. Samples and Resources
1. THE SPECS
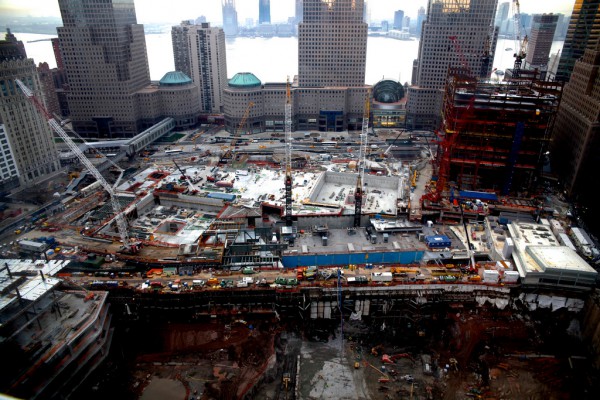
NYC Ground Zero / Freedom Tower construction
View from 35th floor Millenium Hilton. The construction goes on almost 24/7.
via Thomas van de Weerd, 4.06.2010
What are they? Where are they located? Why do we use them? What do they contain?
As with cost control, the most important decisions regarding the quality of a completed facility are made during the design and planning stages rather than during construction. It is during these preliminary stages that component configurations, material specifications and functional performance are decided. Quality control during construction consists largely of insuring conformance to these original design and planning decisions.(Hendrickson, 1998, Ch.13)
The Project Manual
The Specifications are part of the information turned over in the Contract Documents. The Contract Documents are usually delivered in several parts:
- The Drawings
- The Project Manual
- Conditions for Construction Conditions to the Contract / General Conditions (how the project will be delivered and documented)
- Bid Requirements / Bid Forms / Instructions to Bidders
- Specifications (optional)
- The Specifications (sometimes included in the Project Manual)
- Other supporting documentation (addendum, scope sheets, contracting requirements, schedules, etc.)
Specifications are only one part of what may be issued as a Project Manual (often inaccurately referred to as the Project Specification), which can also govern how the project will be administered during construction.
Going forward, we will focus on the Specifications.
The Specifications (or “architectural specifications” or “construction specifications” or regularly just “specs”) are part of the contract documents that complements the drawings by detailing the materials that are to be used, the installation to be followed, and any inspections or quality control procedures to be followed. They are usually created or compiled by the design team, however others may be involved.
Q1: What documents are part of the Construction Documents in addition to the specifications?
Q2: Who compiles the specifications?
Need for Specifications
Our need for written specifications has grown as project delivery methods have changed over time. From AIA’s Emerging Professional’ss Companion (emphasis mine):
As the art and science of building developed and the responsibility for construction shifted from the designer to a separate contractor, the need for explanatory information in the form of written notes arose. Then,as the complexity of the construction process grew, so did the volume of written notes needed to fully communicate the design intent to the constructor.Ultimately, the notes were removed from the drawings,organized, and placed in a document of their own. Thus, specifications evolved as a way to supplement drawing notations, eliminating the need for large amounts of text on the drawings, which tended to clutter what should be a clear image of the intended construction
See more from the Metropolitan Builders Association of Greater Milwaukee:
Good question.This should tell you everything you need to know about why we want to read the spec and avoid disputes.
Q3: Why is it suggested that a specification be written to the level of a brighter than average seventh grader?
Now on to what information is contained is the Specs.
2. FORMAT
Specifications are usually formatted in three parts:
Part I – General
- Description of work
- Related Work
- Submittals
- Inspection Requirements
- Testing, Certificates, etc.
Part II – Products
- Technical specifications for all materials, equipment, fabrications, etc.
Part III – Execution
- Qualitative requirements for workmanship, methods, etc.
Samples
Here is a sample Project Manual from 2009 that contains Specs:
Spec Selection & Writing Tools
Many material manufacturers and fabricators offer a wide variety of tools to design teams to make it easier for their products to be specified. This screen shot from Benjamin Moore’s industry professional’s resource page (accessed 2.13.18) shows many resources available to architects and interior designers who might be researching paint types, colors, performance, and test results.
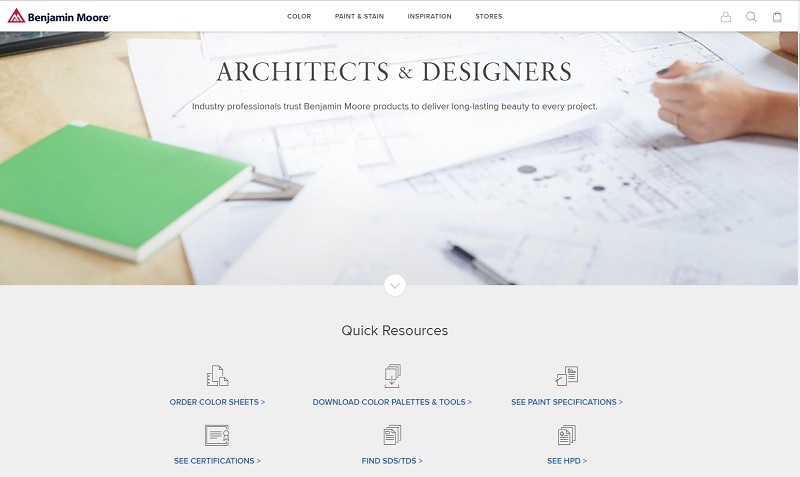
Screen shot from Benjamin Moore’s ARCHITECTS & DESIGNERS page, https://www.benjaminmoore.com/en-us/architects-designers, accessed 2/13/18
Scrolling through their Spec tools, you will find information such as this master file, providing information on paint and other wall coatings to be inserted into a specification.
Benjamin Moore and other manufacturers also provide spec writing tools that produce most of the detail and format that appears in standard specifications based on the products selected.
Performance vs. Prescriptive Specifications
Specifications may be considered either performance specs or prescriptive specs.
Here is a sample of a performance spec from the above sample:
For floor penetrations with annular spaces exceeding 4 inches in width and exposed to possibleloading and traffic, provide firestop systems capable of supporting floor loads involved, either byinstalling floor plates or by other means. (078413 Penetration Firestopping .1.3)
Surface Closers: BHMA A156.4, Grade 1,Provide type of arm required for closer to be located on non-public side of door, unless otherwise indicated.1.Manufacturers:a. LCN Closers; an Ingersoll-Rand Company (LCN);Model 4040 for doors under 40inches in width. Model 4041 for doors over 40 inches in width. (087100 Door Hardware 2.9)
Q4: Define performance specification and explain why one might be preferred.
Q5: Define performance specification and explain why one might be preferred.
3. AVOIDING CONFLICTS
Many conflicts can be avoided by simply reading the full specifications, checking them against the latest contract drawings, and asking questions about any conflicts you see before moving forward (make sure the answers to these questions are put in writing and kept on file).
Sometimes conflicts arise after a contract is signed due to inconsistencies between the drawings and specifications. Often in these cases, one party believes that their scope is governed by what they have seen in the drawings and the other party believes that the scope is governed by what they have seen in the specifications – but the documents do not match. In these cases, the relative importance of the documents may decide who wins the dispute.
In general, remember the following:
- Agreement governs over specifications
- Specifications govern over drawings
- Detail specifications govern over general specifications
The Agreement is your contract. Since it governs over all, be sure to check there first. Look for a “Coordination Clause.”
4. SUBMITTALS
What are submittals?
Submittals are prepared by the contractor and include shop drawings, product literature [cut sheets], or actual samples of products to be installed; reports from independent testing agencies; operating instructions and maintenance manuals for installed equipment; and warranties from product suppliers and equipment manufacturers. The submittals… become part of the permanent record of the project. Some or all of them are eventually given to the building owner for operations purposes.
via The Architect’s Handbook of Professional Practice, Volume 1, 2001, pg 611.
Submittals are reviewed by the architect or appropriate design consultant and the final approval should come (in writing) from the prime design professional, usually the architect.
Just because a document is sent in (submitted) to the owner or design team, does not make it a submittal. Common examples would be contracts, schedules, requisitions, etc. These documents may go to the owner’s team for approval but are not typically considered submittals.
During the approval process, typical submittals may be include the following:
- Cut sheets / Data sheets
- Shop drawings
- Calculations
- Samples
- Color charts
- Mockups
After the physical completion of work, additional documents are created to explain or document the final installation. These documents are typically considered submittals and include the following:
- Operation & Maintenance (O&M) Manuals
- As-built drawings
- Testing & Balancing reports
- Warranties & Guarantees
These after installation document srae usually still considered submittals because they require design team review against the drawings and specifications for approval. If work as installed is found to be in conflict with the drawings or specifications, remediation may be required by the contractor.
Remember:
Shop Drawings, Product Data [cut sheets], Samples, and similar submittals are not Contract Documents. The purpose of their submittals is to demonstrate for those portions of the work for which submittals are required by the Contract Documents the way by which the Contractor proposes to conform to the information given and the design concept expressed in the Contract Documents.
via The Architect’s Handbook of Professional Practice, Volume 1, 2001, pg 827.
Q6: How do submittals differ from contract documents even though they require approval by the Architect on behalf of the Project Owner?
5. SPECS AND ENFORCEMENT
A well written spec should be clear, concise, and contain objective goals. A poorly written spec may include requirements that are actually unenforceable – too vague or subjective to be properly judged. Beware of phrases similar to the following:
- Best quality
- Best workmanship
- Free of defects
- Everything required for a complete project
Specs are one of many ways that quality control is maintained on a project.
- Drawings & Specifications
- Experience Requirements
- Field Supervision
- Design Team / Owner Inspections
- Third Party Inspections
- Factory Inspections
- Certified Laboratory Test Reports
- Mock ups
- Supplier / Vendor Inspections
- City Inspections
- Warranties (implied and express)
6. Samples and Resources
A selection of current, approved U.S. construction criteria is available through the Whole Building Design Guide (WBDG): https://www.wbdg.org/ffc/federal-facility-criteria
For example, the US DDOT’s publicly available 2009 Manual on Uniform Traffic Control Devices for Streets and Highways can be found here: https://www.wbdg.org/ffc/dot/fhwa-criteria/mu-tcd