Problem 3
Description –
Problem 3 involved the making of regular flats and curved flats Ā for a comedy show that will be slamming the door. My main goal was to produce the flats that won’t wobble when the door is slammed. Our solution for this was creating hollywood flats Ā that would be attached to steel framed pass through jack. When considering the jacks we needed one that does not obstruct the actors of the show when exiting through the door. The second goal for this project was producing the molding for the curved flats. The initial thoughts Ā of the group was either to build it or buy from a custom molding shop. Our approach to creating the curved moulding was to make a curved beam. strips of 2×4 were ripped on end and then glued against a form with a 3 ft radius. In attempt to recreate the molding i created a routing jig that went along the curve of the beam. The process in trying to recreate the desired molding was very time intensive to get started and would be difficult for students in city tech scenery crew.
Analysis –
This problem can relate to a real world situation by having to create a prototype to test if your solution is viable option Ā before making the final decisions. In many instances you would create a scale model for the jack prototype but due to our materials chosen we couldn’t do so Ā and meant we had to build it full size. The difficulty of making curved molding was more than enough reasoning to try and find an alternative solution.
Application –
I learned that when testing the prototype is important to try and replicate the situation as close as possible to the original solution. When testing the jack, not having a flat the full 12 ft in the shop meant that we needed to use standard 4×8 flats Ā to get the right height. Our jack was not built to support the flats in the alternative method. When the testing began we had significant movement at the top of the flat. Before the testing we should have thought about the other pieces needed to get an accurate test. The molding as a great chance and try and come up with a unique solution. While the project was very time consuming its had many chancesĀ of troubleshooting your approachingĀ having to make minor changes to the jig. the curved piece was gradually trimmed into the rough shape and then final pass for theĀ groove of the molding profile.Ā


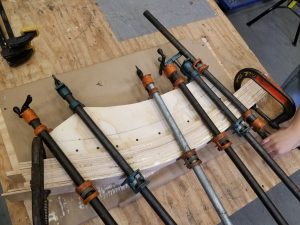



