For problem 4 Chris and I were tasked with building two pieces from the play dog fight, a rolling counter and a platform bed. The rest of the set was being built by Showman Fabricators. Both pieces needed to be on casters and rolled around scenery elements on stage. The challenge for this problem was not the bed platform, it was the rolling counter. The bed is essentially a platform that is elevated and has pipe attached to it, it was not a very big deal to us, however the counter has to be free standing held up on two sides with nothing aiding it in the middle. For our first test we looked at what kind of caster solution we can use to hide the casters on the bed platform. We arrived at wagon breaks that retract and extend up and down with 3/8″ casters on the end. When they need to be moved they extend in the back of the platform and retracted when the platform is in place. For the rolling counter we were mainly concerned about it being able to withstand the weight of our actor. For our test we took 3 4×8 5/4″ platforms and joined them together with bolts and 5/4″. We were very worried that it would not withstand weight but it did very well. The 4×8 platforms were also close to our actual dimensions for the platform so it was a very successful test. We also attached casters that were omnidirectional to the the counter to see how it moved and it also went well. In case the 5/4″ failed we also planned to do a rabbet joint for the platforms to ensure extra security for the joining of the two pieces. Both pieces were to also be skimmed with 1/4″ Masonite to allow for the blue paint. We learned about how to tackle a problem as a team from different perspective and testing solutions. Managing our time appropriately was key, we had a lot of ideas initially but if something worked we immediately latched on to it rather then test every possible solution. Managing and outsourcing builds and communicating with other companies on load in times and etc is something we also learned about, as well as Showman the famous scenery shop.

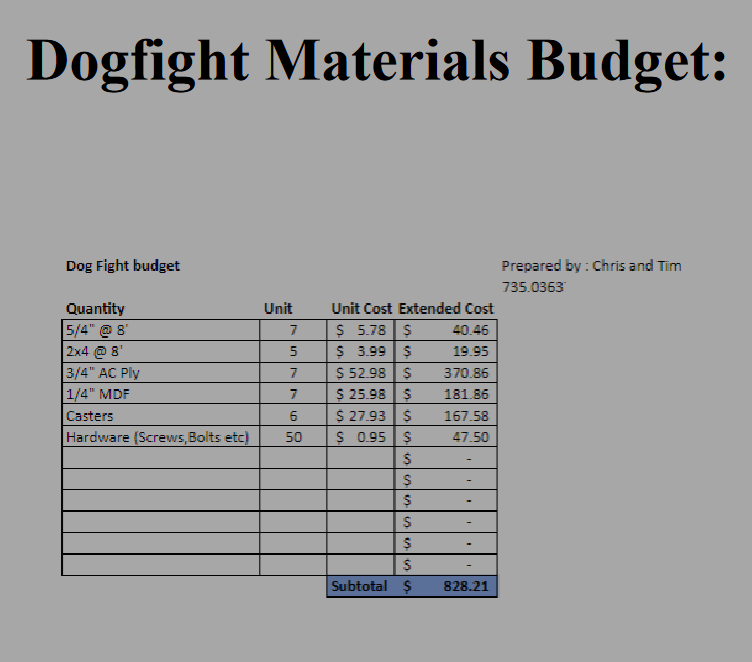
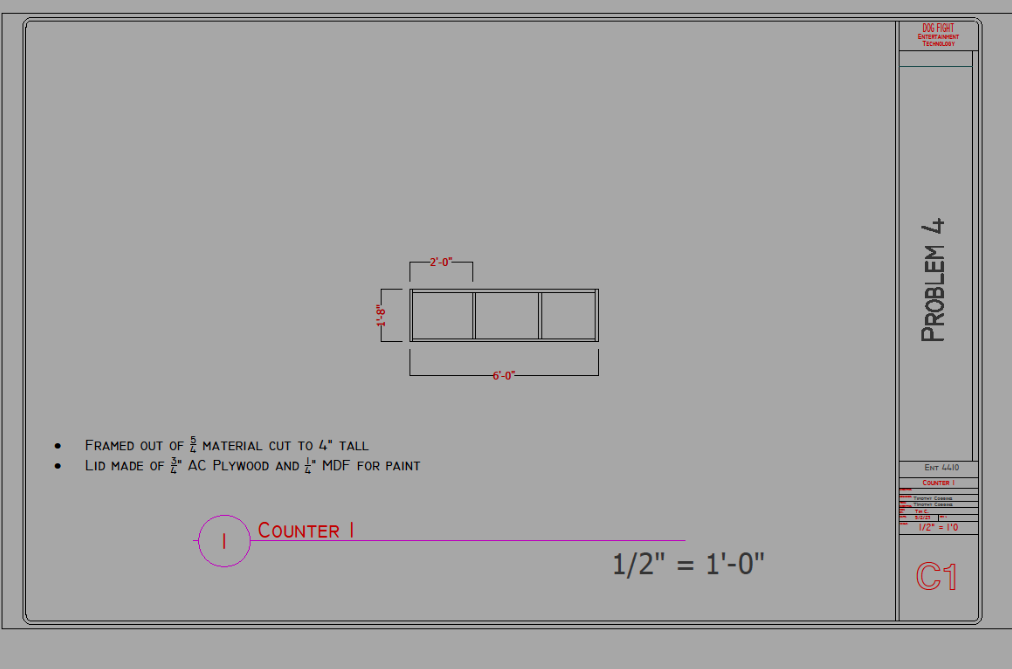

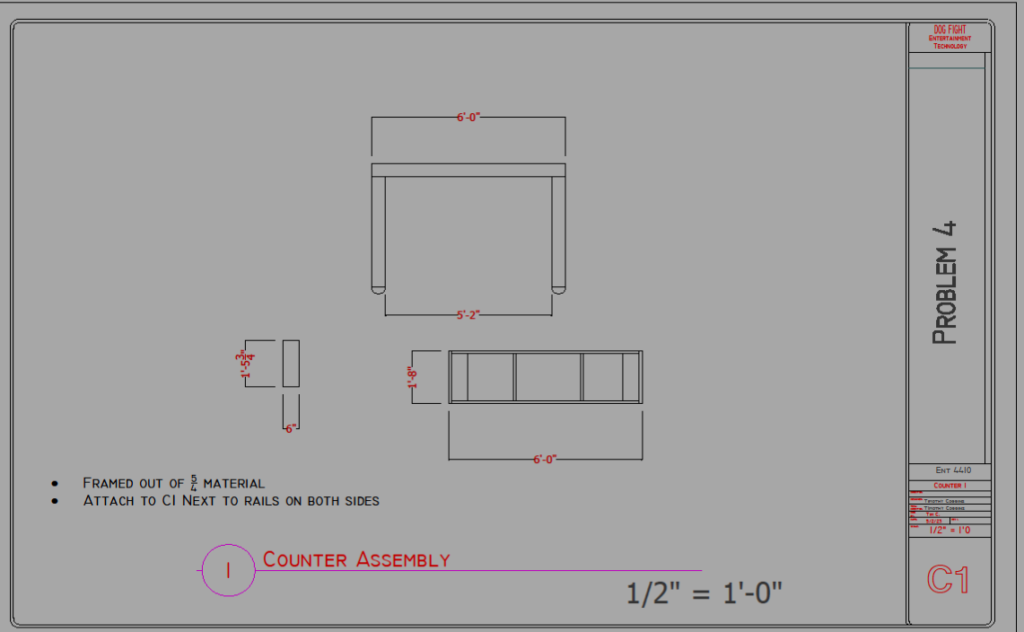