Conceptually, our beach cleaning robot design is based on an existing beach cleaning robot called “Hirottaro 3” [1]. Hirottaro 3 is a beach cleaning robot that removes debris from loose and dry sand using a broom and bucket method as shown in the image below.
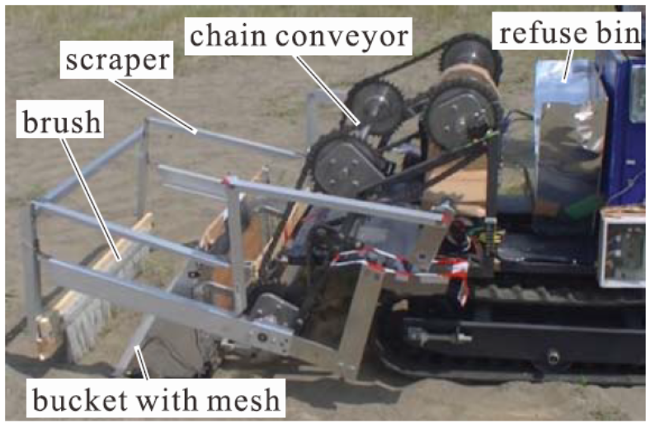
Figure 1: Debris Collection Mechanism. Image credit [1]
However, for our robot design, we will not be using this method exactly. The reason is that the broom method requires the robot to stop, perform a broom sweeping motion into the bucket, and then resume, which consumes a lot of time and energy.
The following figure illustrates this.
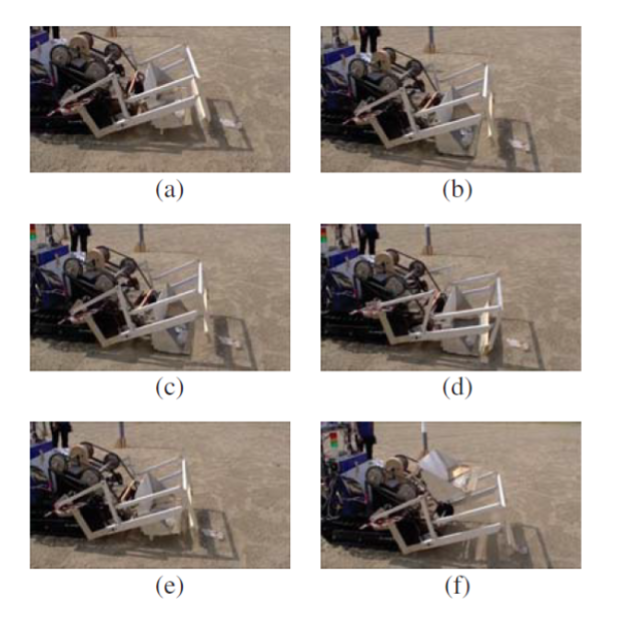
Figure 2: Trash Collection Mechanism in Motion. [1]
This method greatly reduces the efficiency of the robot because it increases the duration of time required to perform the task of cleaning the beach. Additionally, constantly starting electric motors is inefficient as in-rush currents are generated due to high starting torque conditions leading to power losses.
To avoid this, the broom mechanism used in Hirottaro 3 will be replaced with a rolling broom mechanism. This mechanism will involve a broom-like roller that spins in a direction that causes sand and debris to be flicked into the bucket. The image below illustrates this mechanism.
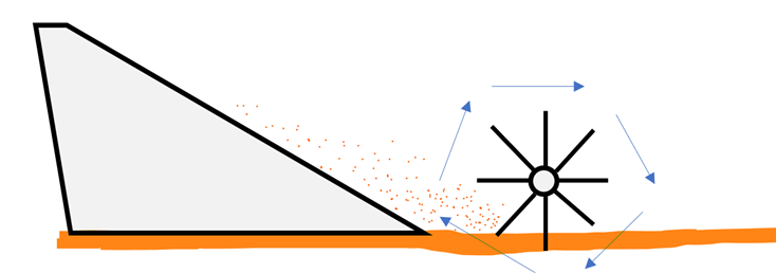
Figure 3: Rolling Broom Mechanism.
Basic Operating Principles of the Rolling Broom Mechanism
- The rolling broom mechanism is rotated using the same electric motor used to drive the robot itself.
- Roller chains and sprockets are used to transmit power to the rolling broom.
- The rolling broom’s rotational speed can be made faster by reducing the number of teeth on the sprocket. This ensures that the rolling broom can rotate quickly even if the robot is moving relatively slowly.
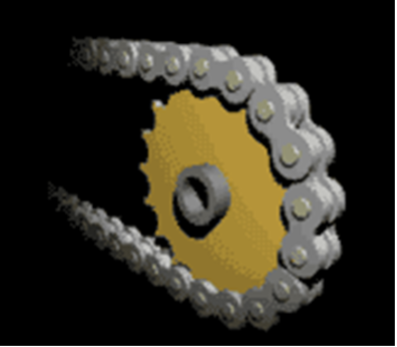
Figure 4: Rolling Chain and Sprocket Mechanism.
Image credit: Wikipedia.com
The collection bucket has a mesh base. As sand and debris are deposited into the bucket, the mixture gets sieved. This happens due to the additional vibration caused by the rolling broom’s physical interaction with the uneven surface of the beach. The vibration is transmitted through the shared frame between the collection bucket and the rolling broom.
Basic Operating Principles of the Collection Bucket Mechanism
- Maximum collection capacity can be detected by the use of a strain gauge as well as an ultrasonic sensor. The strain gauge can be used to detect weight, while the ultrasonic sensor can be used to detect maximum volumetric capacity.
- Once maximum collection capacity is detected, the robot stops, and the collection bucket is transported via a conveyor belt system into a position where it can dump the trash into a larger bin.
- The collection bucket then returns to its collecting position and the robot resumes its operation.
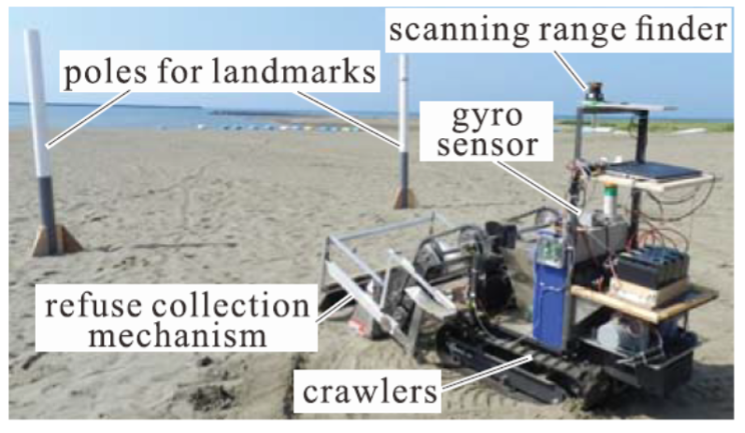
Figure 5: Complete Overview of Hirottaro 3. [1]
Our robot will be designed with similar crawlers as the ones used in Hirottaro 3 in the image above.
Crawlers like these are ideal for uneven surfaces and sandy conditions such as those typically found on a beach. Using dual electric motors, one to drive each crawler, directional changes in the robots’ movements can be made effectively. In fact, using this system, the robot can rotate in any direction while maintaining a stationary position.
Path Planning
Figure 5 shows poles used as landmarks. These poles are there for the robot’s guidance system to have references that allow it to determine its path. The following image illustrates how we intend to use this idea.

Figure 6: Poles placed at the end of the beach furthest from the water.